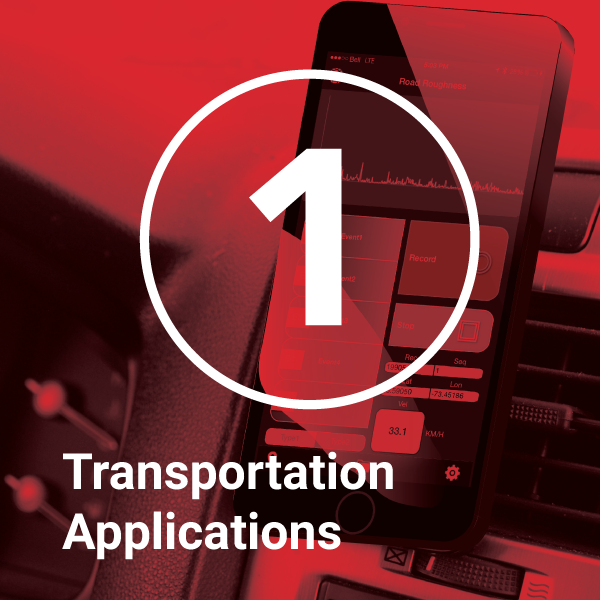
Municipal Roadways
Managing pavement assets today is a dynamic activity, and the need to have information at the ready is not just for large agencies. Data elements to meet funding programs, preservation based management approaches, cross asset optimization, and extreme weather events impact current maintenance activities and future plans.
rMD offers simple and practical approach these needs, and enables agencies to quickly, easily, and effectively review their current condition, run budget scenarios, develop works programs, and export information for use across departments. Buy combining this decision aiding app to RUBIX with field collection apps such as rRuf and rInspector, municipal users are armed with a complete turnkey solution to manage their pavement networks.
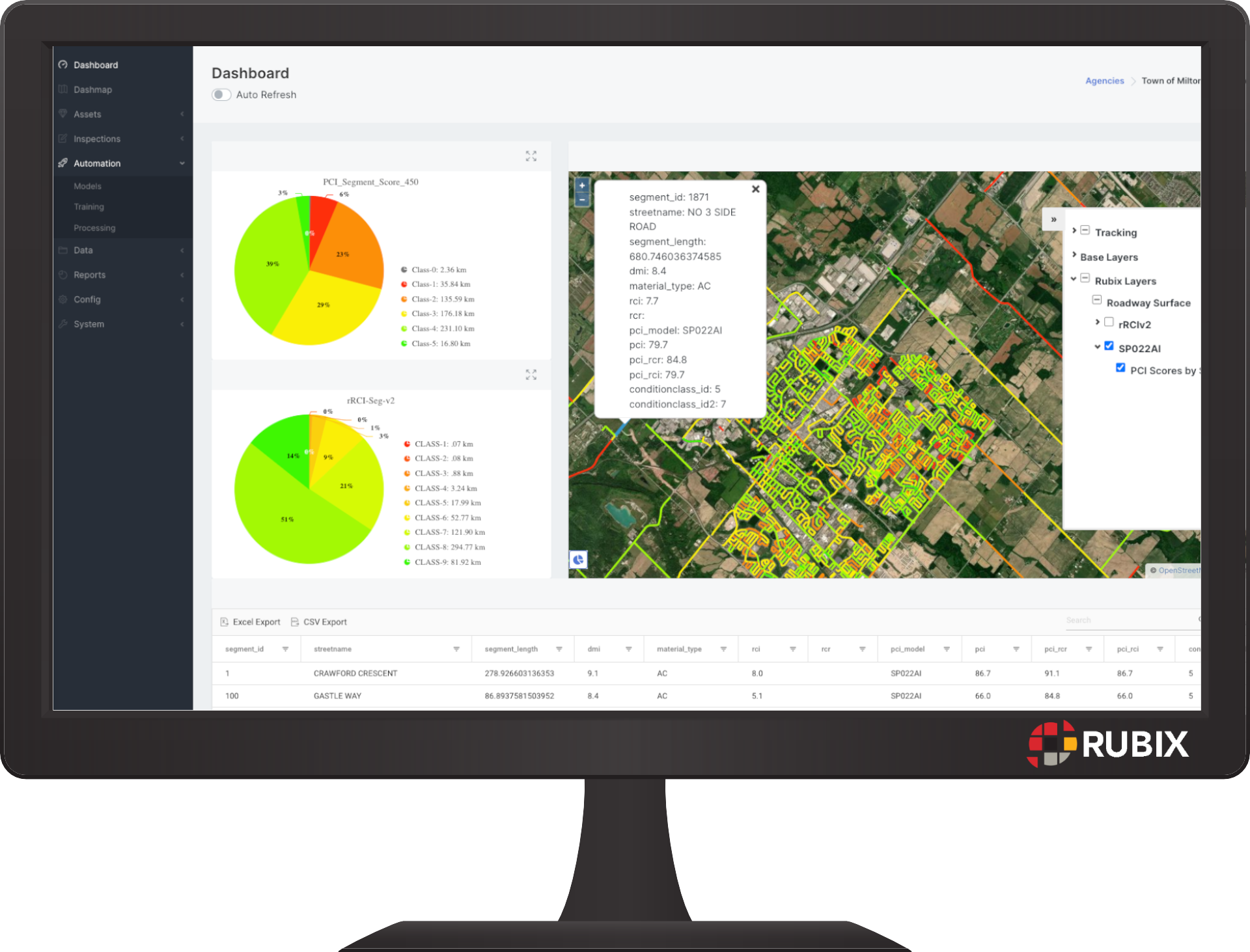
Shown above, Automated PCI Results for Road Network
Low Volume Roads
Gravel roadways continue to be a challenge when it comes to proactive management and maintenance. Typically, gravel roadways are managed in a reactive mode, either based on major weather events, or citizen complaints. Conventional pavement management tactics are difficult to implement as gravel road structures are dramatically impacted by rain and snow events.
Rival offers a variety of solutions from its core RUBIX platform to conduct roadway condition surveys, and many specifically design for low volume roads. The goal of these solutions is to provide simple condition assessment capabilities with rapid data turnaround. Standards such as PASER or customized business rules are used to log condition data on such roads while keeping mobile.
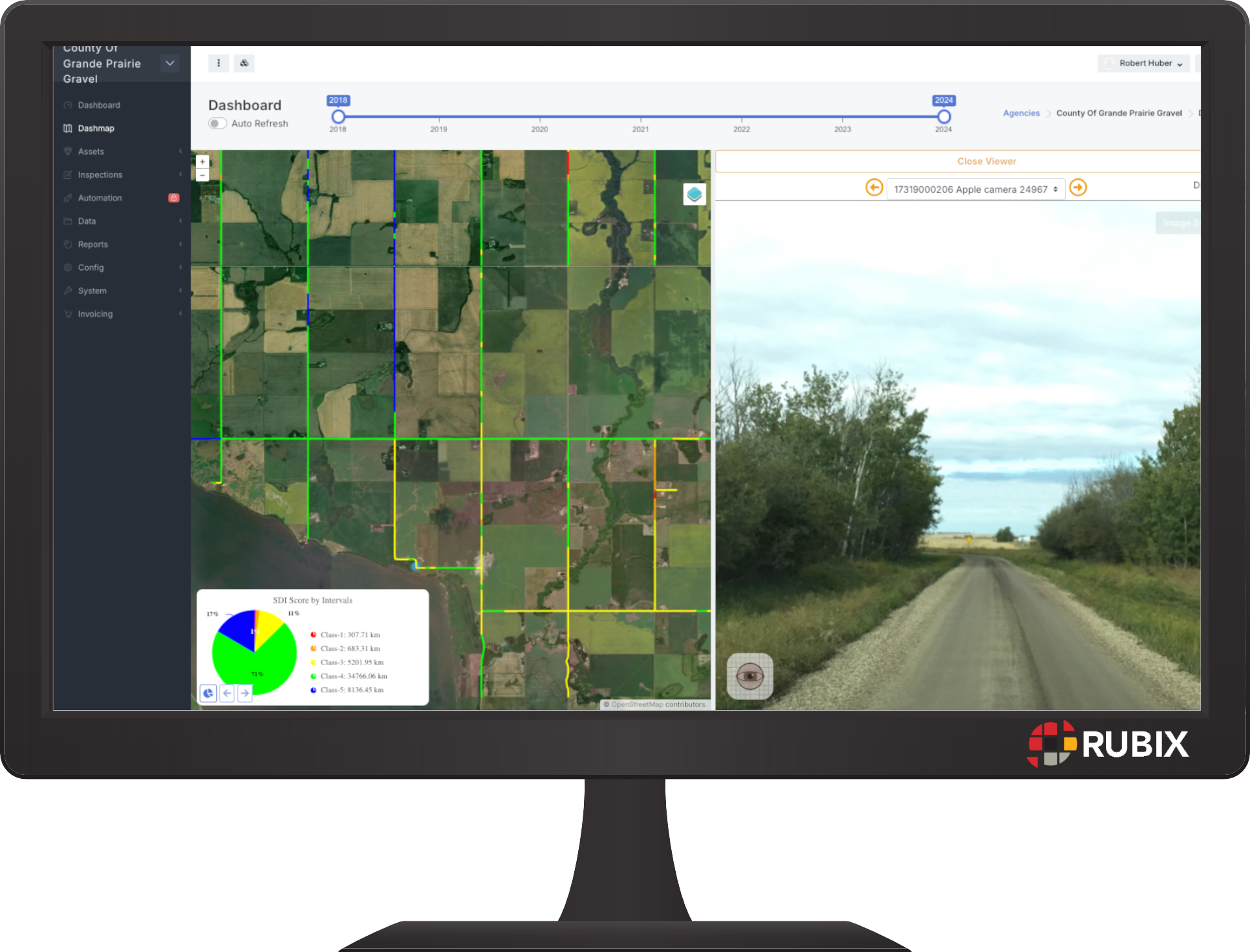
Active Transportation
Implementing an effective management program for trails and/or sidewalks poses several unique challenges compared to other transportation assets such as roads or bridges. Primary, these networks are used for pedestrian use, and various usages (walking, biking, wheelchairs, walkers, etc.). These types of usages are what RSI uses as key factors to its turnkey, Sidewalk/Trail Management approach.
The RUBIX platform facilitates data collection, visualization, analytics and job prioritization for trail and sidewalk asset management projects.
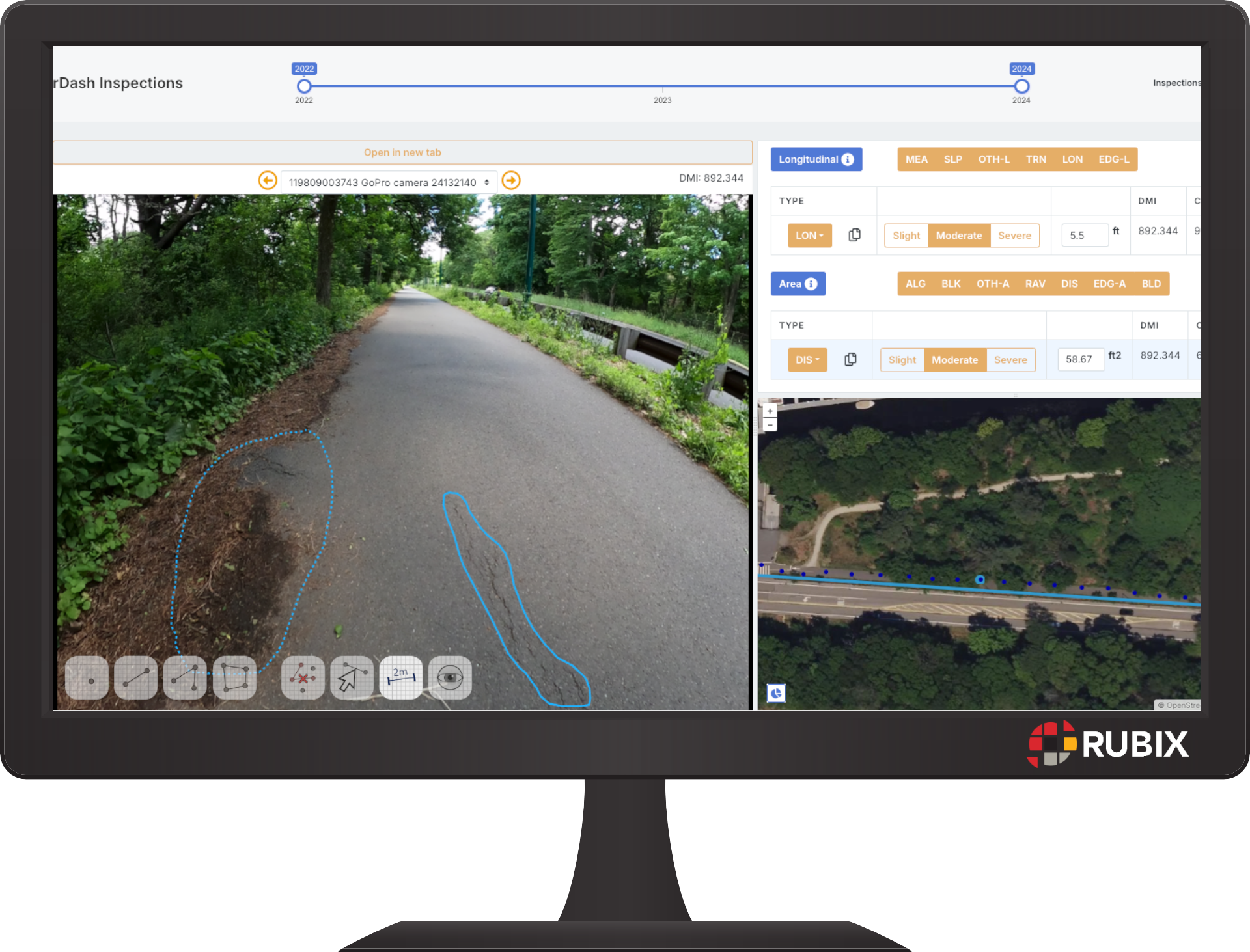
Bridge and Culvert Inspections
Culvert and Bridge inspections have become more efficient with the use of tablets, allowing inspectors to streamline their workflow. Using the rInspector app, inspectors can conduct detailed assessments of culverts by capturing high-quality images on-site and recording key information in real-time. This digital approach not only improves accuracy but also saves time by eliminating the need for manual paperwork. Once the inspection is complete, the collected data and images are seamlessly uploaded to RUBIX. This integration enables immediate access to the inspection data, helping teams quickly analyze conditions, generate reports, and schedule maintenance as needed.
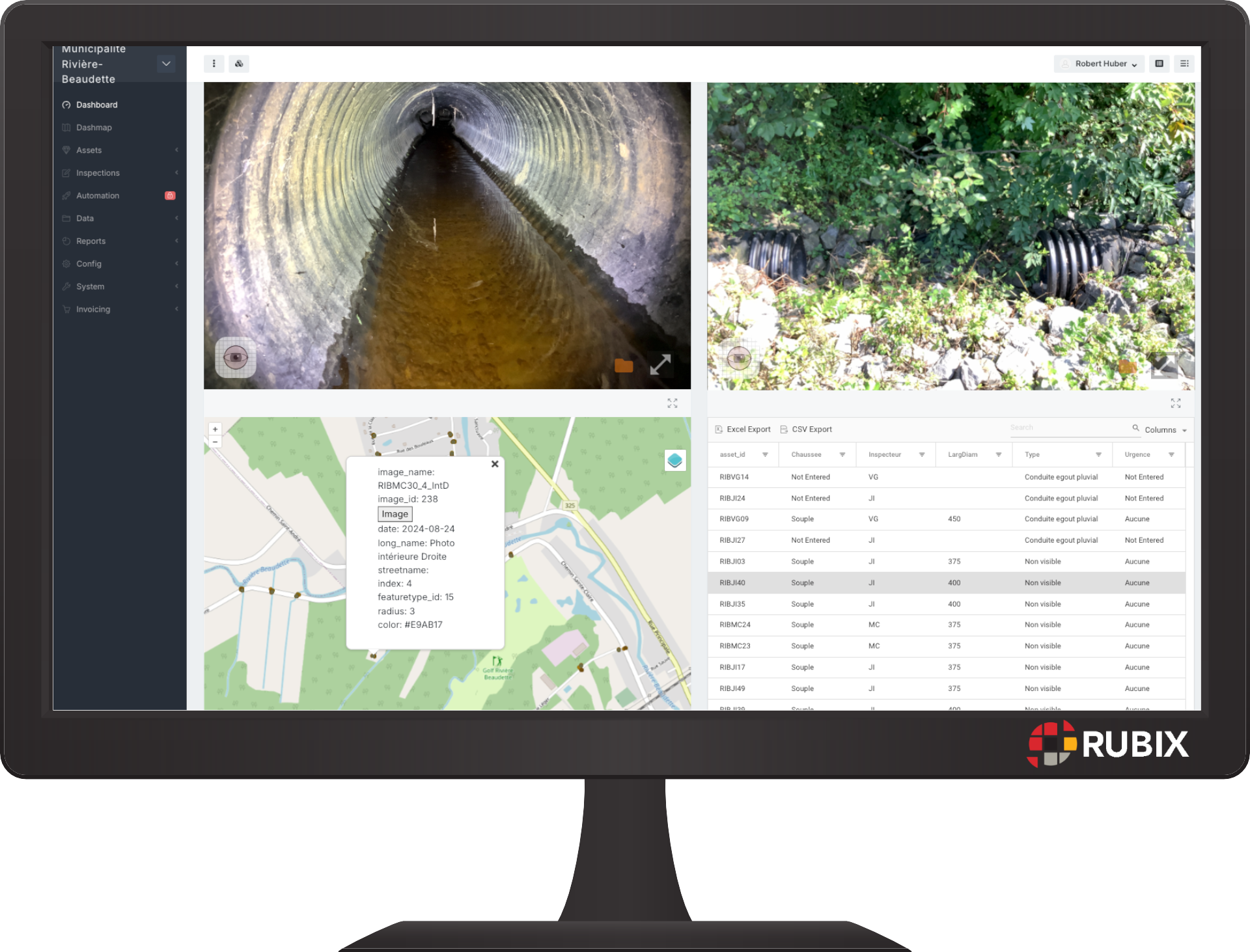
Sign Detection
Sign detection and classification using AI from mobile images has significantly advanced road and traffic management systems. By capturing images with mobile devices or action cameras, AI algorithms can automatically detect and classify various types of signs, such as traffic signals, regulatory signs, or hazard warnings. These AI models are trained to recognize different sign shapes, colors, and symbols, ensuring accurate identification even in varying weather or lighting conditions. This automation reduces the need for manual inspections, increases data processing speed, and allows for real-time updates in navigation systems or infrastructure databases. With the ability to track the location of detected signs, this technology enhances road safety and maintenance by ensuring proper visibility and compliance with traffic regulations.
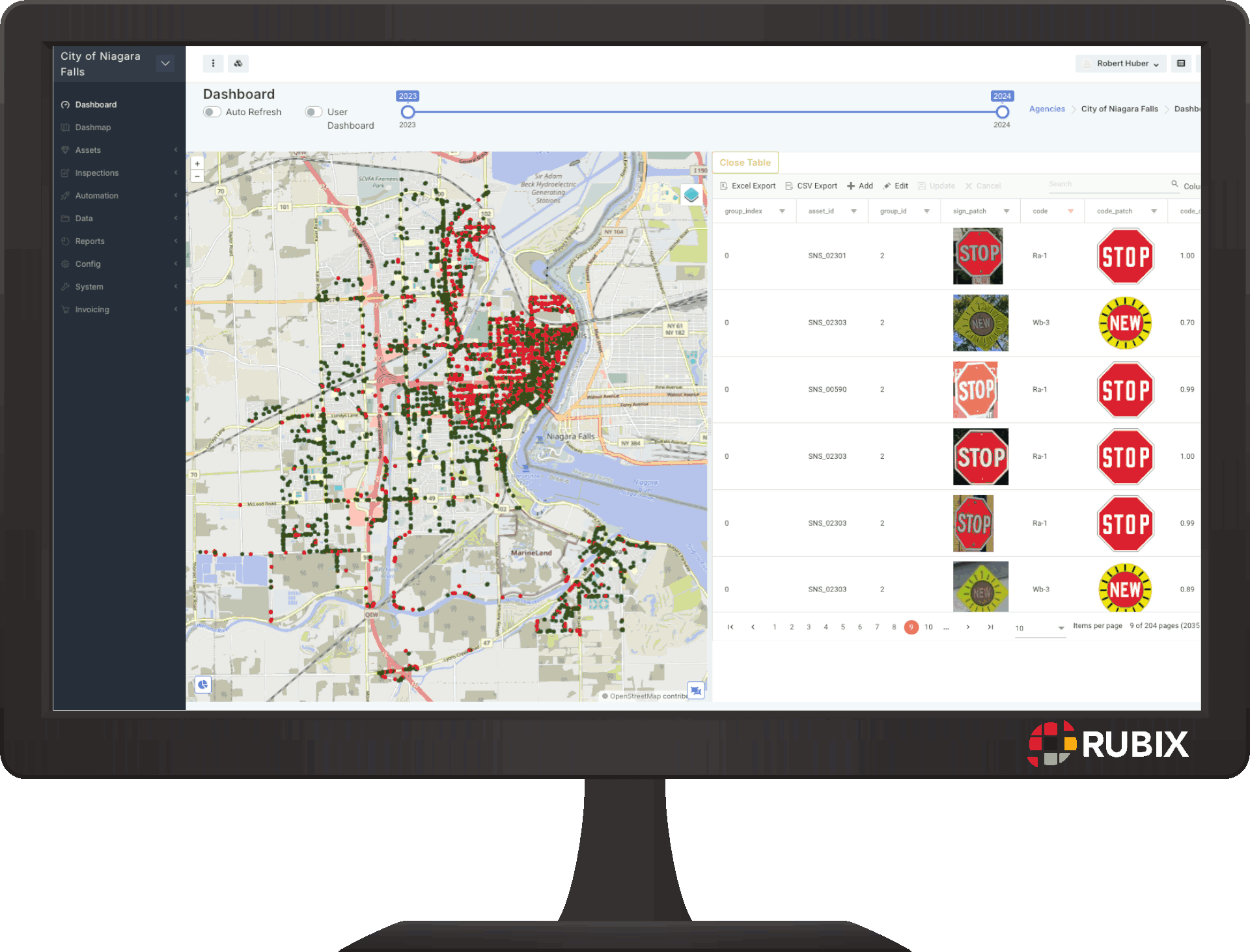
Parking Lot and Facility Inspection
AI-powered condition inspection of parking lots and associated infrastructure, such as drainage systems and walkways, offers a transformative approach to asset management. By analyzing images captured via smartphones or action cameras, AI can detect surface damage like cracks, potholes, and erosion, as well as evaluate drainage effectiveness by identifying blocked or damaged grates. This technology allows for rapid, consistent, and large-scale inspections, reducing the need for manual assessments and enabling more timely and cost-effective maintenance strategies. For more traditional inspections, manual surveys can also be conducted using specialized data entry forms on a tablet.
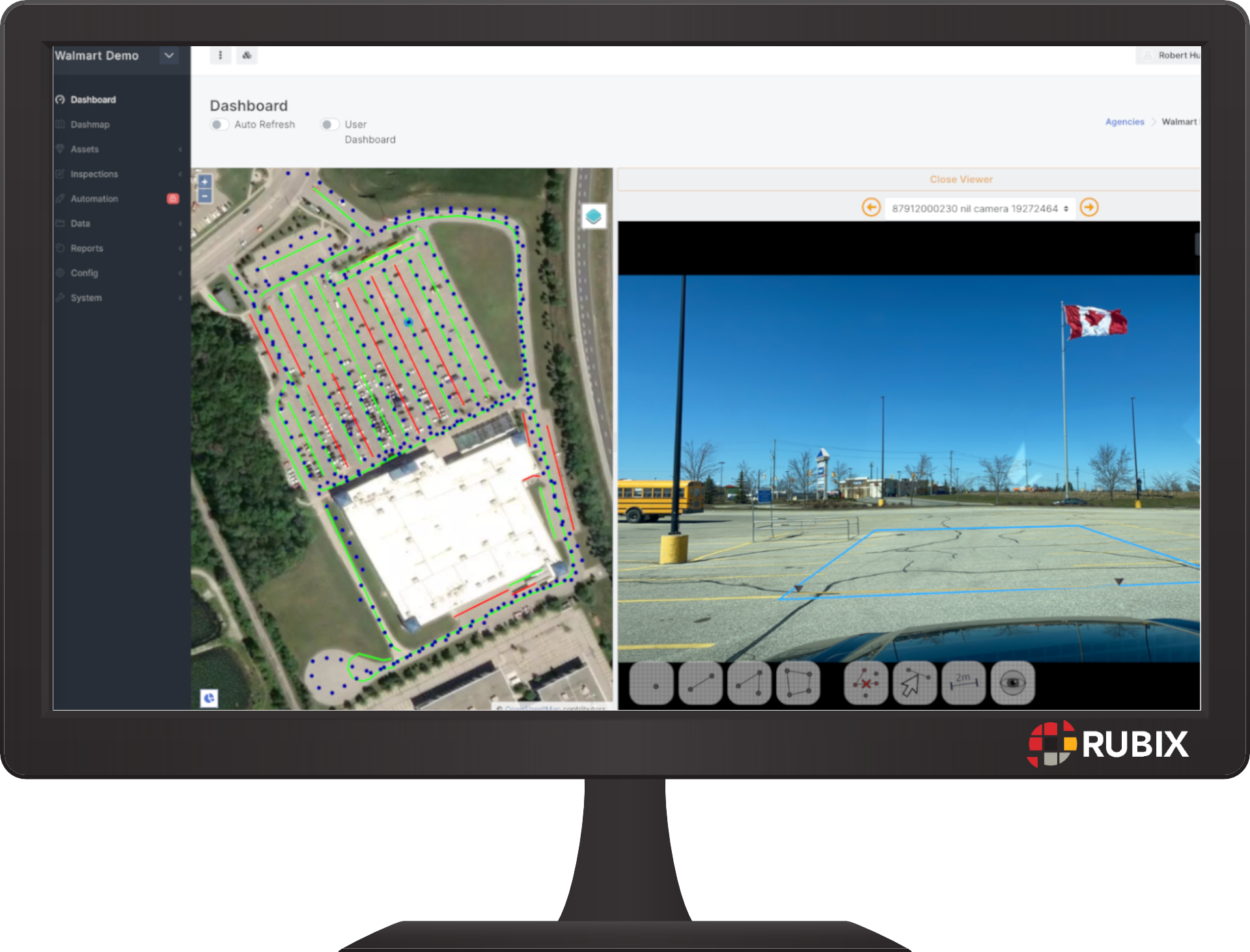
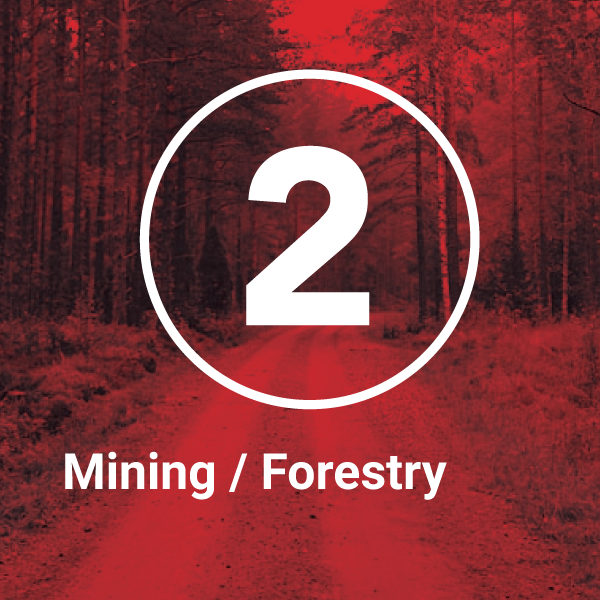
Haul Road Condition Monitoring and Management
Haul Road operations require smooth roads but find it difficult to transform road defects into an effective, reactive road maintenance program. Haul road networks need to be maintained to a functional performance level that optimizes safety, haulage production as well as vehicle operating and maintenance costs. To achieve these goals a road management strategy, which uses ongoing data collection to determine haul road defects and model the operating environment to create a proactive approach, could generate significant cost savings.
The Haul Road Integrity solution has been designed and developed to continually collect data and quantify conditions into an overall Haul Road Integrity Index (HRII) by combining road roughness, speed and grade data into an aggregated index. Our data analytics can be tailored to provide reports to the mine operator which will illustrate operational data to determine if trucks are achieving optimal speeds and cycle times on grades based upon haul road design parameters. Additionally, continual data collection provides historical information to analyze haul road conditions for the prediction of road maintenance intervals for stable and reliable roads to optimize mine production, reduce vehicle operating costs and maximize maintenance equipment utilization. The fundamental purpose of our services is to reduce cost per hour, increase tonnes per hour production thus decreasing overall cost per tonne.
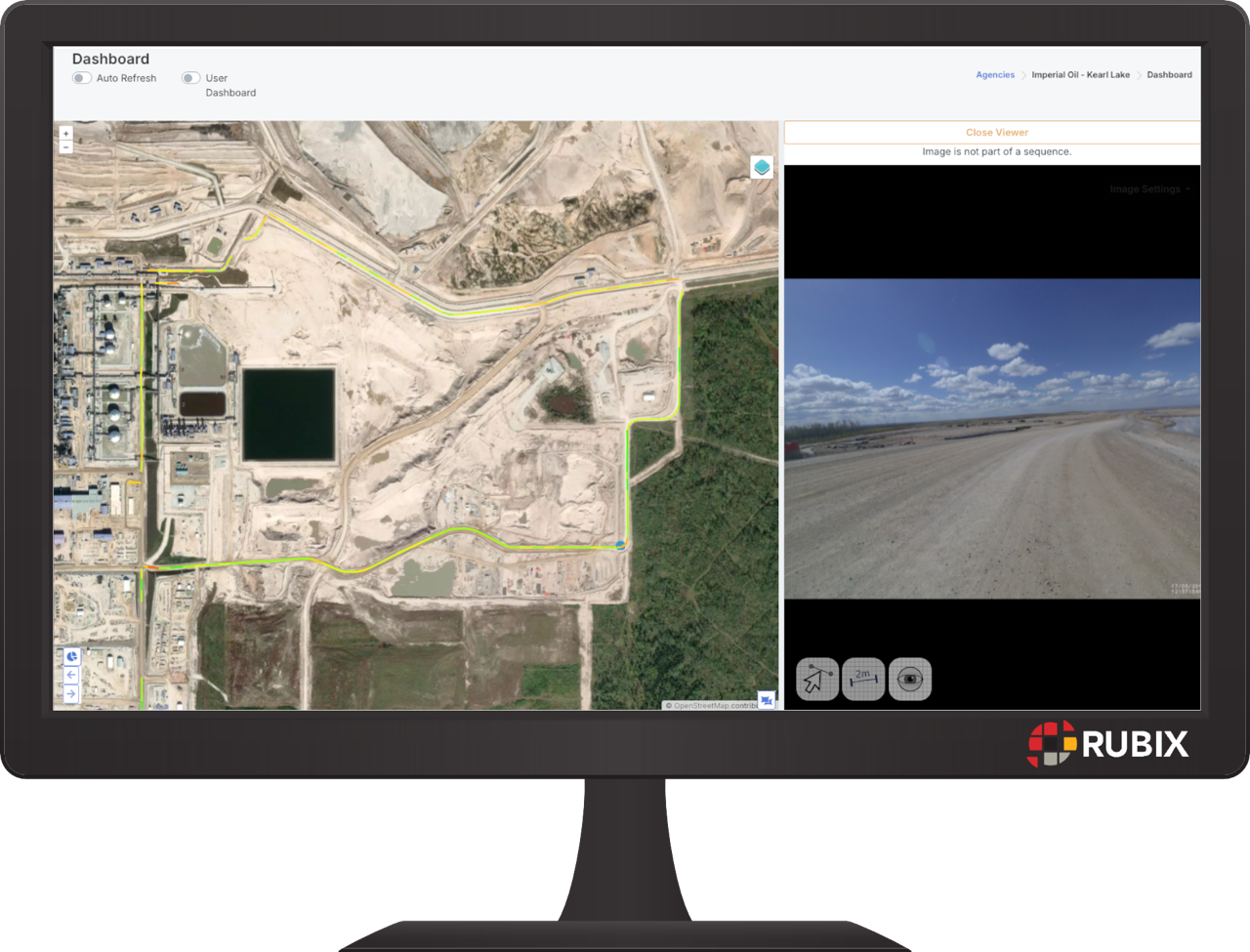
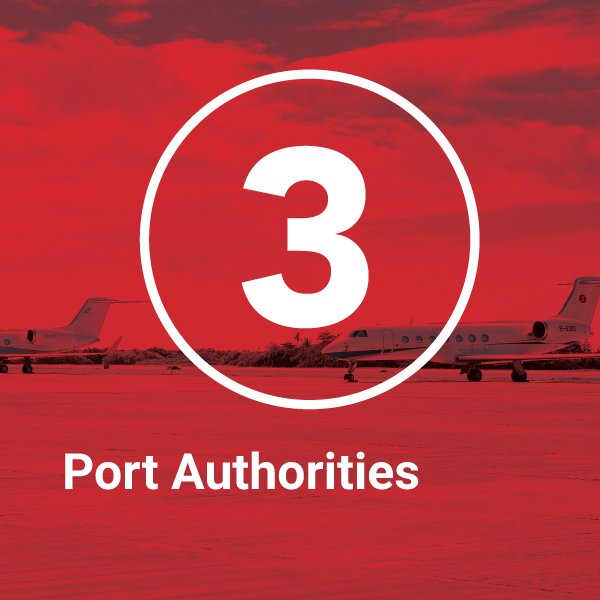
Storage Facility Inspection and Management
In 2016, the port of Montreal was looking for a solution to manage its main road, transit and storage assets. It required a centralize solution where all inspection information is stored and made available to the different stakeholders which include port authority managers as well as terminal operators. It was also looking for a solution for better guidance and planning of long term maintenance and rehab budgets for those assets.
The port of Montreal selected RUBIX to inspect and manage the condition of surface condition information within the facility. Asset condition information can either be visualized globally for the whole port authority or specifically for individual terminals. It uses RUBIX rMD to manage the long term rehabilitation budgeting and planning of its assets.
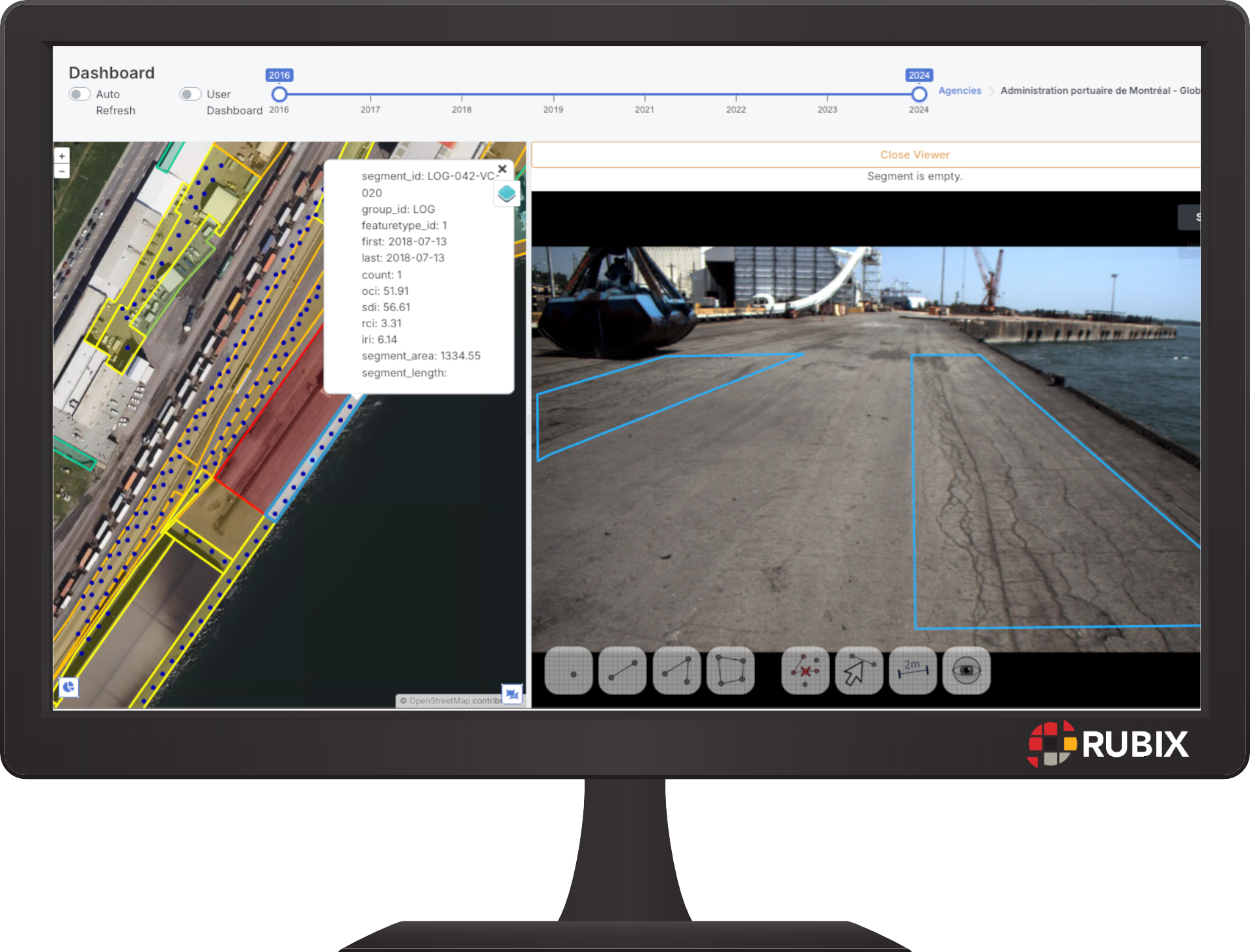
Airports (Ground and Air Side Inspection and Management)
Using images to extract defects on airport runways and tarmacs has revolutionized the inspection process for large surface areas. High-resolution imagery, captured by mobile imaging technologies, allows for the precise identification of surface defects such as cracks, depressions, or debris. RUBIX can analyze these images, automatically detecting and classifying defects and rolling up data to industry standard KPI such as ASTM-D5340. Additionally, the spatial tracking capability of defects and inspection samples ensures that each defect is accurately mapped to its location on the runway or tarmac, crucial for large-scale inspections. This spatial data enables teams to monitor problem areas over time, prioritize repairs, and efficiently plan maintenance, ensuring both safety and cost-effectiveness.
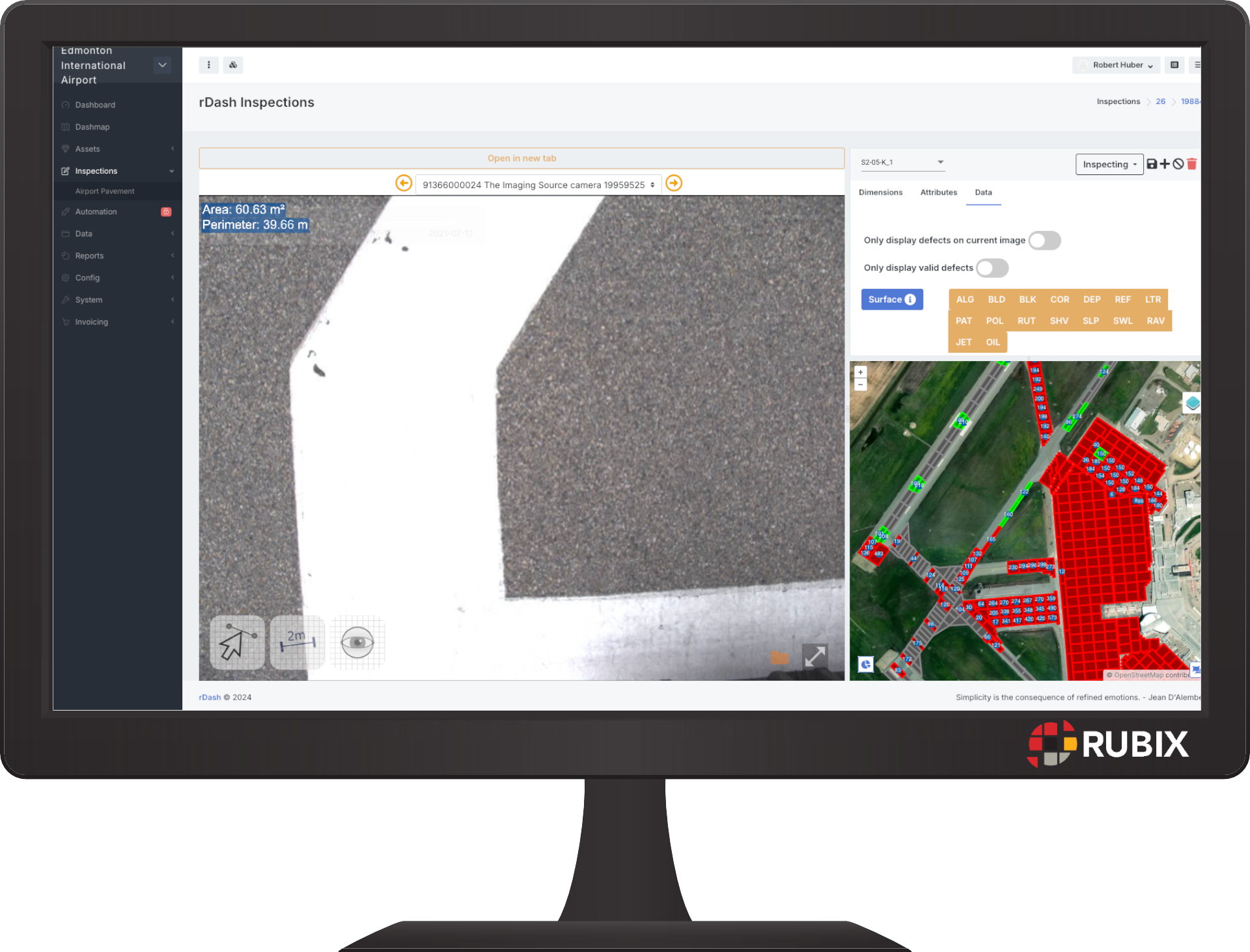
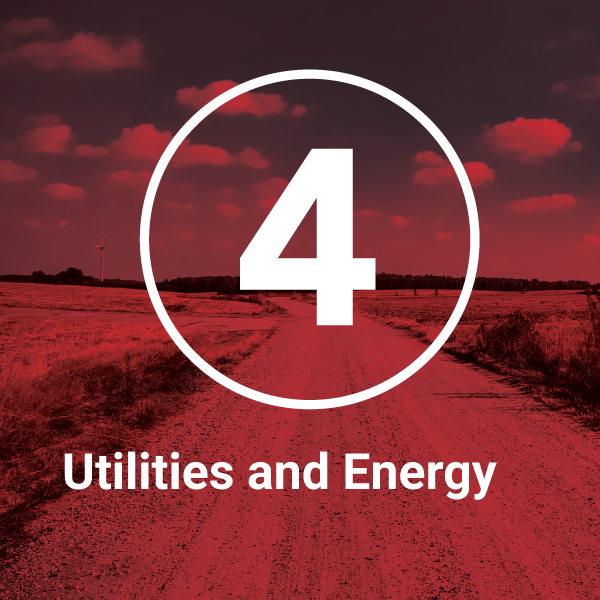
Pipeline Pre /Post Haul Road Analysis
The data collection team surveyed 438 miles of paved haul roads in Spreads 4–6 of the DAPL Project, spanning North Dakota, South Dakota, and Iowa. High-resolution pavement images and mobile Light Detection and Ranging (LiDAR) data were gathered to record road conditions prior to the start of construction. Once the imagery and LiDAR data were collected, our team analyzed 10% of each road for condition assessment and Pavement Condition Index (PCI) scoring. The process followed the ASTM International Standard Practice for Roads and Parking Lots Pavement Condition Index Surveys (ASTM-D6433-11) to document individual distresses and calculate PCI scores. Each sample area was approximately 25 ft. wide by 100 ft. long (2,500 sq. ft.), as per the ASTM D6433 standard.
The mobile capture vehicle was equipped with a Trimble MX-8 mobile LiDAR unit and a downward-facing camera system that captured 12 ft. x 12 ft. images at 1.5-megapixel resolution. For this project, over 385,000 pavement images were taken, and mobile LiDAR was used concurrently to detect and measure existing rutting on the roadways.
It’s important to note that certain PCI defects cannot be confidently captured using only downward images, due to various factors. Issues like bleeding, pumping, and polished aggregate require visual inspection in the field. In these instances, a technician in the capture vehicle used a tablet to manually record such defects on the spot. These supplementary entries were linked to each sample location and uploaded to the overall database for final PCI computation.
All results were entered into RUBIX for PCI computation and to analyze road conditions before and after the heavy equipment and materials were transported for pipeline construction. The information was ultimately used to provide each county with an assessment of road damage caused by the hauling process.
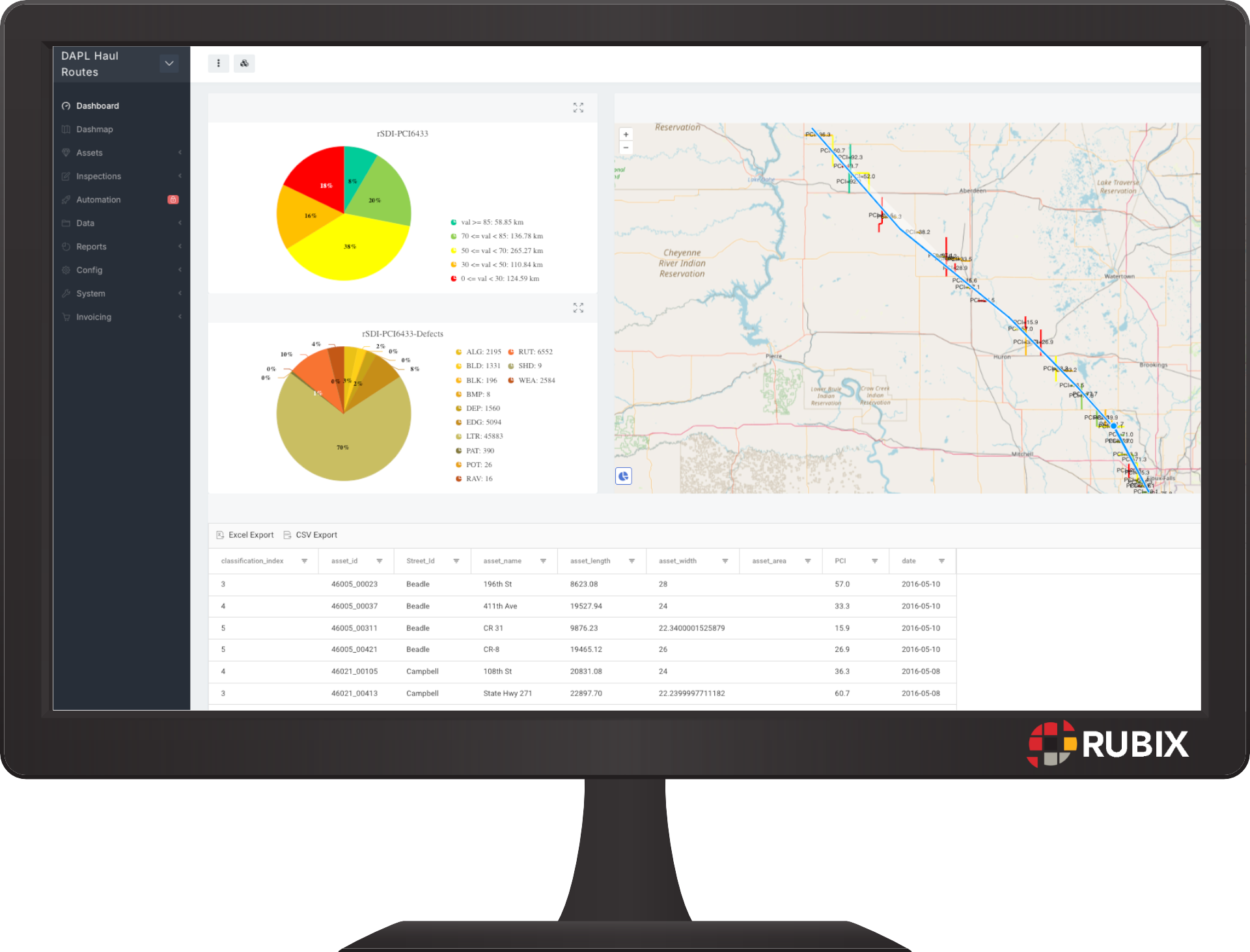
Utility Cut Inspection and Management
The inspection and tracking of utility cuts play a crucial role in holding stakeholders accountable for road damage caused by excavation activities. Utility cuts, made for installing or repairing services like water, gas, or electricity, often compromise the integrity of the road surface. By implementing advanced inspection methods, such as high-resolution imaging and GPS mapping, it becomes possible to monitor the exact location and condition of these cuts. Using tools like RUBIX software, inspectors can document any defects or degradation caused by the excavation, assign responsibility to the relevant stakeholder, and ensure that repairs are carried out to restore the road to its original state. This process helps prevent long-term damage, reduces maintenance costs, and improves the overall durability of the road network. Tracking utility cuts also fosters accountability, ensuring that companies or entities responsible for digging are liable for the repair and restoration of the road, promoting better practices and maintaining infrastructure quality.
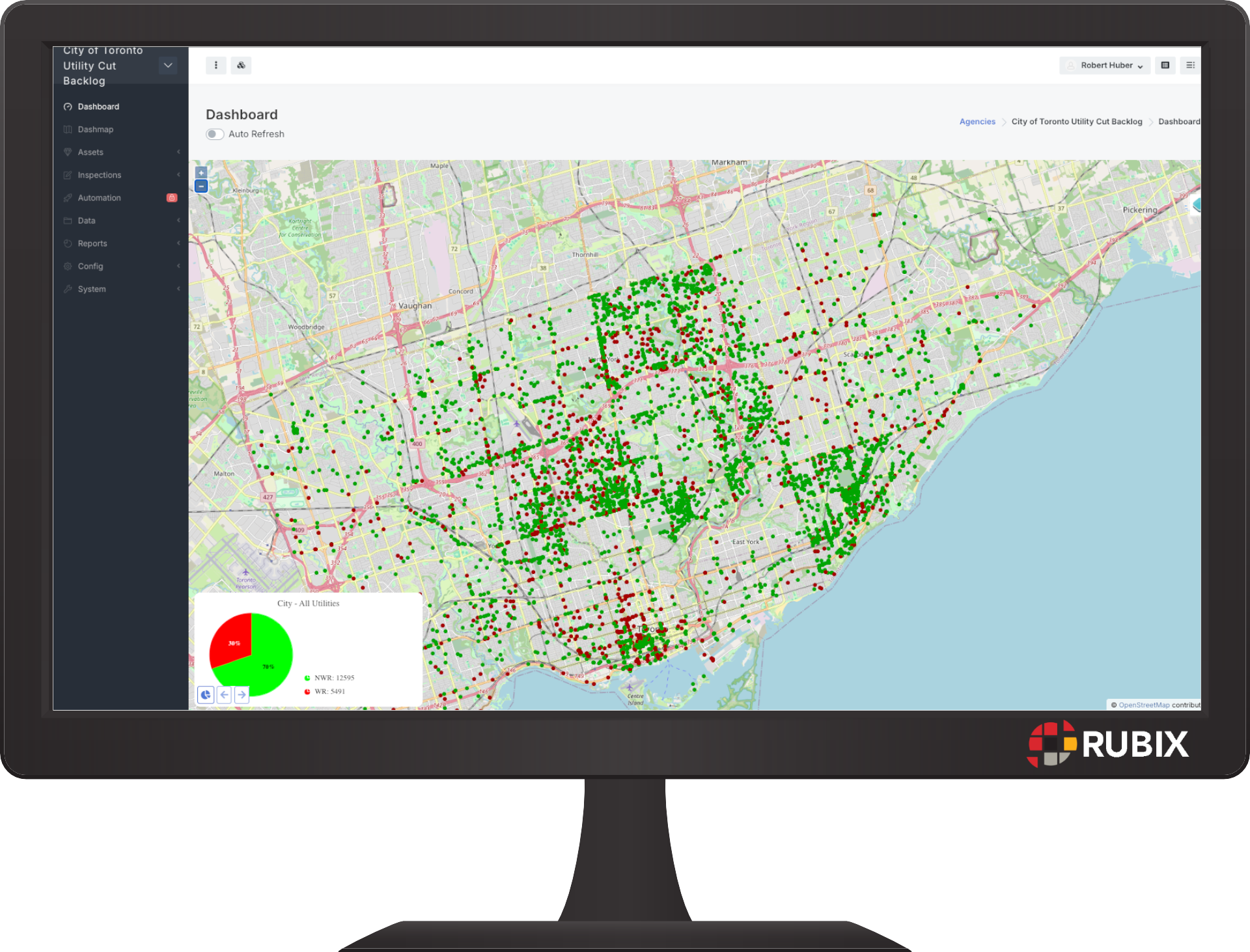
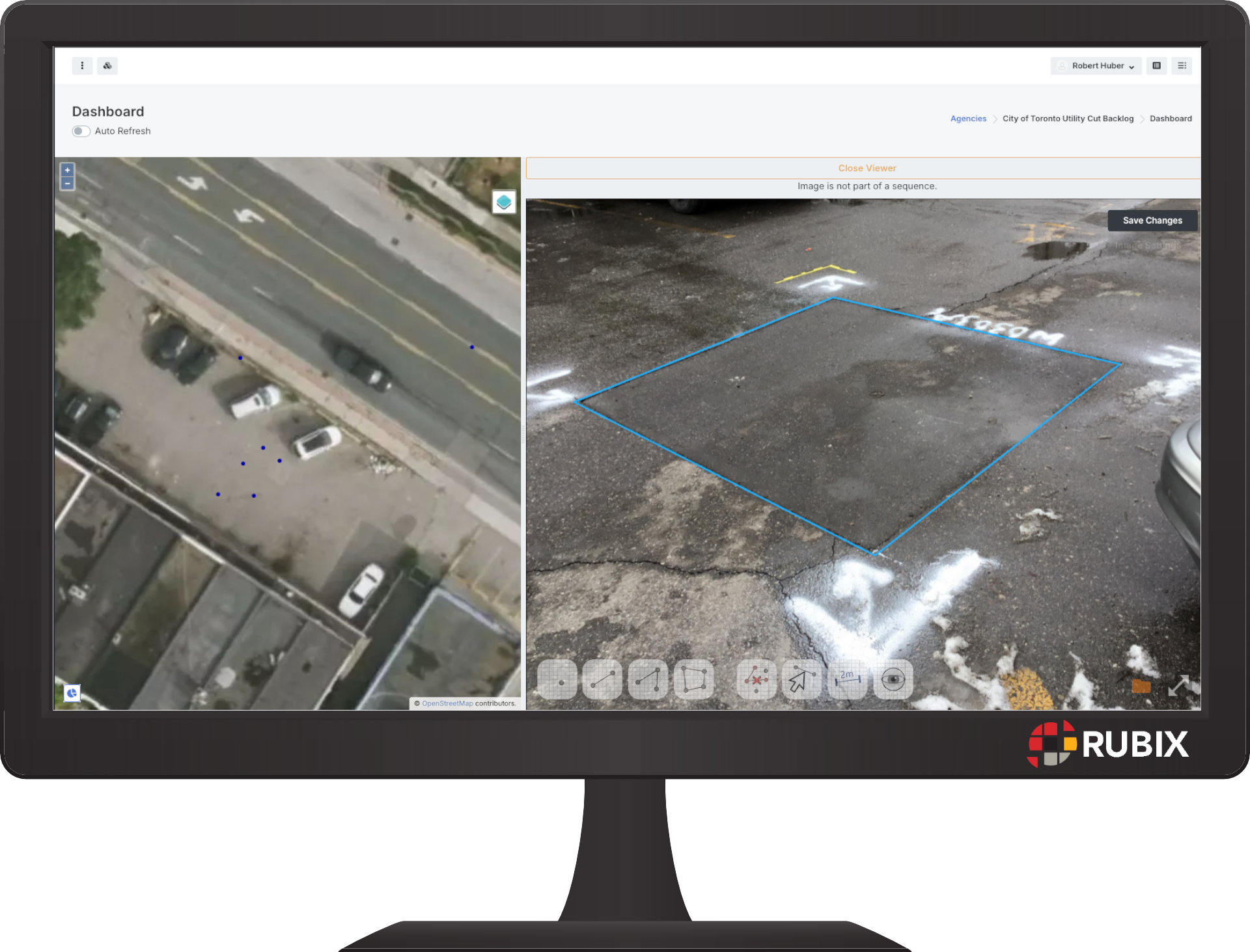